Client Profile
FDA-regulated global pharmaceutical company
Business Challenge
An international pharmaceutical company with multiple plants had several manual processes in place, including hand documentation, Excel spreadsheets and Microsoft Word documents to report and track events, including defects and lab incidents. The inefficiencies were impacting the company’s ability to validate end products and was threatening their compliance with FDA regulations.
Project Objective
A multi-project, multi- quality management systems implementation, including Corrective and Preventive Actions (CAPA) and qualified event module implementation, was integrated to streamline preparation for regulatory audits, supplier quality management, and FDA compliance.
Built-in data collection, document handling, notification and escalation features, as well as training and documentation management, ensured reports, including defect reports and other related CAPAs, were routed for proper resolution, monitoring, and scheduling.
Delivered Results
LABUR’s quality management systems implementation and guideline documentation and training streamlined cross-functional areas of the business to ensure FDA-compliance. This elevated the pharmaceutical company’s brand reputation and integrity, strengthening their international reputation and export business.
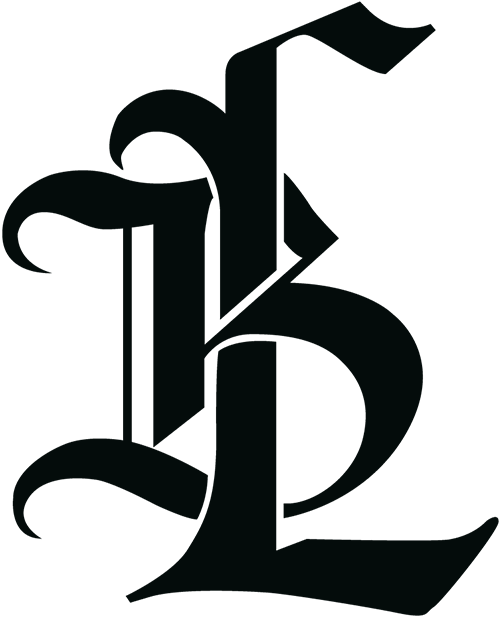